REDBAG 322 – a mixture intended for arranging and repairing floor screeds on rigid bonded substrates, on separating layers (waterproofing, polyethylene layer, etc.), for making sloping floors; for preparing bases for leveling mixtures, or for laying ceramic coatings, for arranging floor structures with water heating inside and outside buildings. Recommended layer thickness from 10 to 80 mm. Compressive strength 25 MPa (M250).
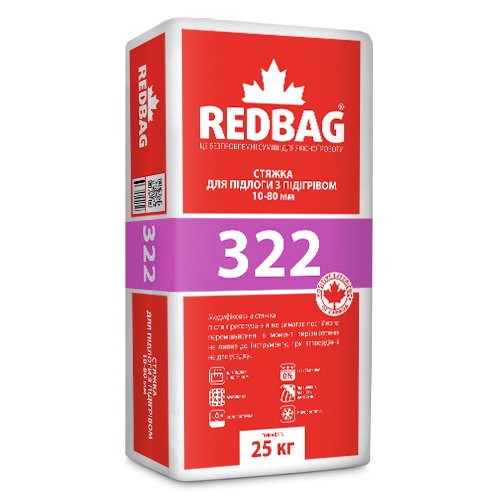
REDBAG 322 SCREED FOR HEATED FLOOR 10-80 mm
Frost-resistant reinforced screed after preparation does not require constant mixing, does not stick to the tool when leveling, and does not shrink when hardening.
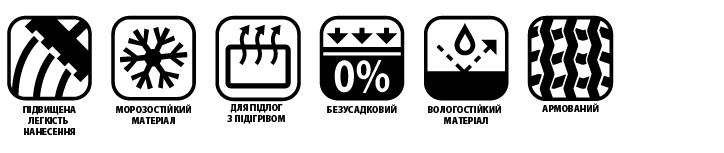
-
Appointment
-
Preparing the base
The base must be dry, not frozen, strong (not less than 25 MPa (M250)), capable of bearing loads, free from dust, dirt, oils, greases, lubricants, old paint residues, wax and other substances that reduce adhesion, have uniform water absorption, and meet the requirements of DSTU-N B A.3.1-23:2013, DSTU-N B V.2.6-212:2016, SNiP 2.03.13-88. Remove weak areas of the base.
In the case when the base has a strength of less than 25 MPa (M250), a separating layer should be arranged using the REDBAG 801 mixture. The separating layer can also be arranged using cardboard, polyethylene, bitumen layers, etc., but in this case the minimum thickness of the screed layer should be 40 mm.
Before arranging the screed on already arranged cement-sand, cement-lime bases, it is necessary to clean it of dust and be sure to treat it with a deep penetration primer REDBAG ADHESIS.
The concrete base should not be subject to shrinkage after arranging the screed, therefore it should be no younger than 3 months from the moment of laying the concrete, and the residual humidity of the concrete should be below 4%. Cast concrete bases have a smooth surface and low moisture absorption, so after cleaning before finishing they must be treated with an adhesive primer for dense, smooth, low or no moisture absorbing bases – REDBAG SUPERSTICK.
-
Cooking method
Pour the REDBAG 322 dry mix into a container with clean water (at the rate of 3.25 - 4.0 l of water per 25 kg or 130-160 ml per 1 kg of dry mix), mix using a construction mixer until a homogeneous mass without lumps is formed. Leave for 3 minutes and mix again.
Do not add other materials to the prepared solution.
Attention! The screed can only be arranged manually and the recommended amount of water can be used when preparing the mixture (arranging using mortar mixing pumps causes an undesirable overdose of water during the preparation of the mixture).
Attention! REDBAG mixtures are created on the basis of modern high-tech recipes using the latest additives from world manufacturers.
When preparing the mixture, use water only in the amount indicated on the package!
-
Work execution technology
Work should be performed at a base temperature of +5 °C to +30 °C. The layer thickness per application should be from 10 mm to 80 mm. When arranging a screed with a thickness of more than 80 mm, it is necessary to add coarse aggregate of fraction from 5 to 20 mm to the mixture in the proportion of 2 parts of the REDBAG 322 mixture to 1 part of aggregate by weight, and apply reinforcement. Reinforcement is performed using a reinforcing welded mesh with a cell size of 100×100 mm and a wire diameter of 2 mm. When performing a screed, it is necessary to follow the rules for arranging expansion joints: structural, insulating and shrinkage. Structural expansion joints should be used in structural joints of buildings and if necessary to reduce the effect of thermal expansion of materials. If such seams already exist in the base, they must be duplicated in the screed. Insulating seams are used to separate the screed being laid from contact with load-bearing and enclosing structures (walls, columns, stairs, etc.), which can limit the deformation of the floor. Insulating seams are made using an elastic layer (foamed polyethylene, thin polystyrene foam). They are also used in places where the thickness of the base changes, in places where different floors meet, and to highlight rectangular fragments of the base in rooms of complex geometric shape. Shrinkage joints should divide the floor into fields with an area of no more than 20 m2 with a side length of up to 5 m indoors, 16 m2 with a side length of up to 4 m outdoors and in rooms with heated floors. In corridors, shrinkage joints are arranged at intervals of 2 corridor widths.
Lay the prepared mortar mixture on the prepared base. When installing a water heating system, fill the heating elements with water before starting work and do not drain for 28 days from the moment the floor is installed, and the mortar layer should be placed 40 mm above the highest point of the pipe with the coolant. After laying the mortar, it must be evenly distributed using a level, vibrating screed or semi-trowel. Final leveling and smoothing should be done using a plastic/polystyrene foam trowel or other tool. The surface should be moistened within 48 hours after completion of the work.
The hardening time of the mortar depends on the temperature and relative humidity of the air. Under normal conditions, namely at a temperature of 20±2 C and a relative humidity of 55±5%, technological movement on the floor is possible 12 hours after laying the screed. The next layer of screed can be applied either in the period from 24 to 72 hours after applying the first layer, or after 14 days! Pouring a self-leveling mixture or arranging coatings using water-based adhesives should be carried out after 72 hours, provided that a heating system is installed in the floor, laying tiles on elastic adhesive TM REDBAG, and arranging coatings using adhesives based on organic solvents - after 7 days. To prevent destruction, the floor heating system can be turned on no earlier than 28 days after arranging the floor.
-
Mixture consumption
1.8 kg/m²* at a layer thickness of 1 mm.
*The mixture consumption depends on the unevenness of the base and the skills of the performer.
REDBAG 322 mixture complies with: EN 13813 CT-C25-F5 and Ts.1.ST2 DSTU B V.2.7-126:2011
Shelf life and storage conditions: 12 months from the date of manufacture, in a dry place, in undamaged original packaging. The date of manufacture is indicated on the packaging.